港聞更多
中國新聞更多
焦點娛聞
體育報導
BEAUTY

探尋初夏的浪漫氣息,瑞士百年奢侈品牌Bally隆重呈獻520限定系列!此次系列涵蓋男士與女士成衣、手袋、鞋履及配飾
探尋初夏的浪漫氣息,瑞士百年奢侈品牌Bally隆重呈獻520限定系列!此次系列涵蓋男士與女士成衣、手…
生活消閒
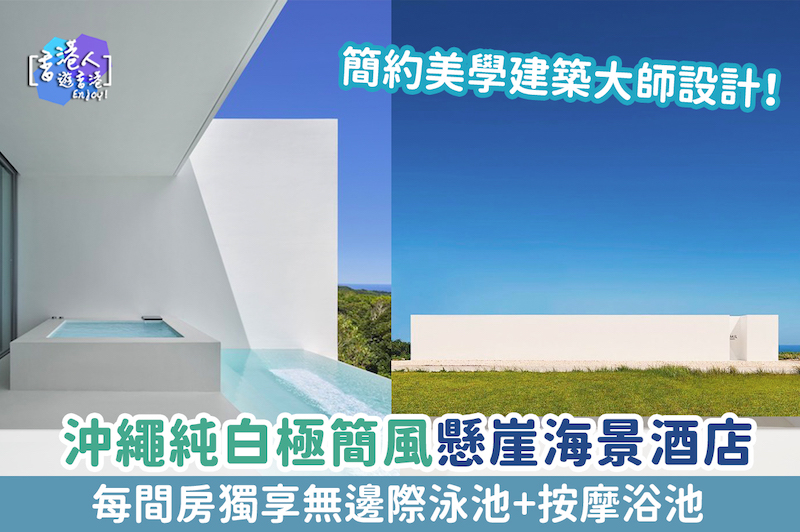
日本酒店:【極簡控注意!沖繩純白極簡風懸崖海景酒店 每間房獨享無邊際泳池+按摩浴池!】- EMIL NAKIJIN
日本酒店推介2024|沖繩純白極簡風懸崖海景酒店 每間房獨享無邊際泳池+按摩浴池EMIL NAKIJ…